GKN Aerospace will be exhibiting an advanced winglet lower skin, produced as part of an advanced winglet development project within the the STeM programme, at the Advanced
Engineering Show, NEC, Birmingham, November 12th and 13th.
The advanced winglet project is part of a £12m Structures Technology Maturity (STeM) programme focused on developing an innovative winglet using fully automated manufacturing
processes. GKN Aerospace leads this project, with Bombardier, Spirit and GE partnering. GKN Aerospace is also providing £1.8m in funding which is matched by TSB (Technology
Strategy Board) support.
|
Manufacture of GKN Aerospace advanced winglet skins at the NCC twin AFP facility.
|
Winglets have become an established feature of wing design because they provide valuable benefits in increased aircraft rate of climb, reduced fuel burn and a reduced noise footprint. The
goal of this GKN Aerospace-led project has been to develop an innovative winglet design and simultaneously progress production processes that will decrease production times and
improve end-product quality, consistency and repeatability.
The advanced winglet’s lower skin is a demonstrator component part with a complex geometry. It has been manufactured from carbon fibre at the UK’s National Composites Centre
(NCC) using the latest automated fibre placement (AFP) technology. Its design has employed the latest software tools and the development process has been used to prove new
modelling, manufacturing and testing methods and advance their readiness for use in future production
programmes.
Rich Oldfield, Technical Director, GKN Aerospace commented: “We face twin challenges to improve airframe performance and to achieve far higher aircraft production rates than have
been achievable until now. We believe the combined focus of the STeM programme will bring benefits on both fronts - and having access to the resources of the NCC is allowing us to work
alongside our partners to progress the technologies and processes that are critical to achieving our goals.”
GKN Aerospace leadership of this STeM programme follows the completion of a ‘Grand Challenge’ in 2011. There, a consortium of 22 companies from across British industry and led by
GKN Aerospace concluded a one year challenge set by the Technology Strategy Board (TSB) on behalf of the Department for Business, Innovation and Skills (BIS). This challenge
required the companies to collaborate to progress innovations in vital composite manufacturing technologies. These would extend the UK’s ability to rapidly and sustainably manufacture
affordable, high-performance composite products - identified as a key global growth market for the future.
GKN Aerospace and Royal Academy of Engineering establish Research Chair with the University of Bath
GKN Aerospace is sponsoring a five year Royal Academy of Engineering (RA Eng.) research chair, based at the University of Bath.
The Royal Academy of Engineering/ GKN Aerospace Chair in Composites Analysis represents a combined investment by the University, the Royal Academy of Engineering and GKN Aerospace. It aims to develop a suite of analytical methods to optimize the efficient use of fibre-reinforced composite material, with the goal of improving the quality, performance and speed of production of high-value composite structures - such as those used in aerospace.
Professor Richard
Butler, who leads a team of researchers at the University, has been nominated for the new chair. Professor Butler has a track record in the analysis and optimisation of aerospace composites. He also has an established relationship with GKN Aerospace, having undertaken an RA Eng industrial secondment with the company in 2011. At that time Professor Butler supported a number of the company’s composite research and development projects, including work to develop novel manufacturing processes to produce a large aircraft wing spar; and creation of an ultra-efficient ‘laminar-flow’ wing design. The continuation of these activities now forms the basis of the new
research chair’s work. |
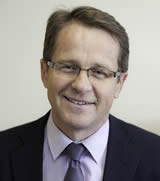 |
Professor Richard
Butler |
Rich Oldfield, Technical Director, GKN Aerospace explains: “The advantages of composite structures are thoroughly proven. However, there remains much to gain from improving production processes to increase the speed and consistency of manufacture and to reduce production and material costs. The work of this research chair at Bath University will be of critical importance to the future success of the UK composites industry - as well as to the long term market position of GKN Aerospace. The results we achieve will strengthen the UK’s broad industrial research landscape through the involvement of the National Composites Centre and a variety of UK-based academic networks.”
|